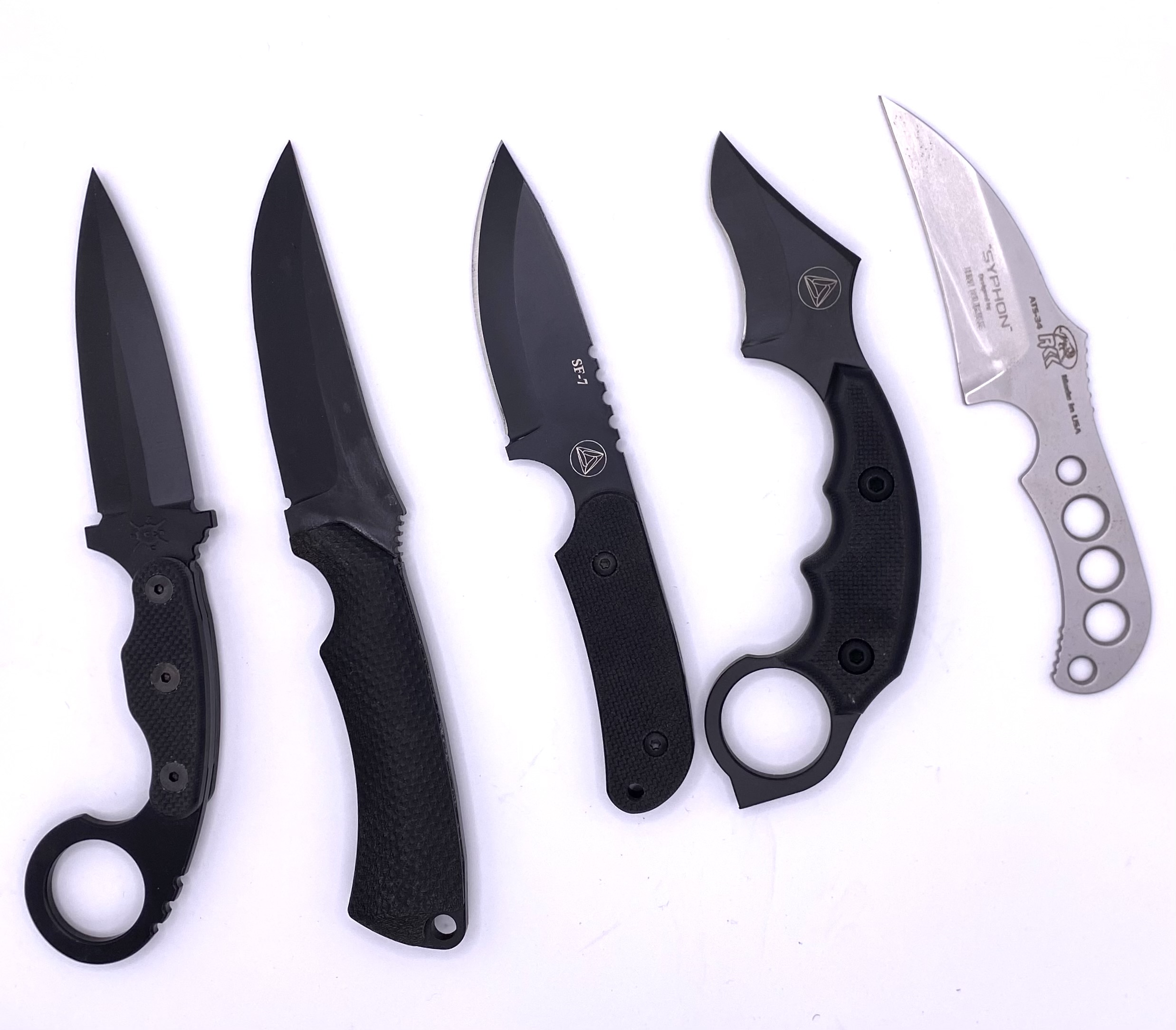
When making custom knives, various materials can be used for the blade, handle, and other components. The choice of materials often depends on the intended use of the knife, the desired aesthetic, and the maker’s preferences. Here are some common materials used for custom knives:
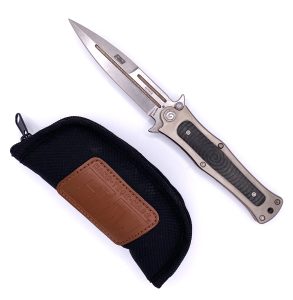
Blade Materials:
- Steel Alloys:
- Carbon Steel: Offers excellent sharpness and edge retention but is prone to corrosion. It requires regular maintenance.
- Stainless Steel: Resistant to corrosion and requires less maintenance, but it may be harder to sharpen than carbon steel.
- Tool Steel:
- D2, O1, A2: High carbon tool steels known for their durability and resistance to wear.
- Damascus Steel:
- A composite of multiple layers of steel, often folded and patterned for a distinctive look. It can combine the properties of different steel types.
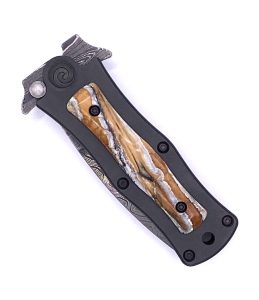
Handle Materials:
- Wood:
- Exotic Hardwoods (e.g., Cocobolo, Rosewood): Offer a natural and aesthetically pleasing look.
- Micarta: A composite material made from layers of linen, canvas, or paper impregnated with resin. It’s durable and provides a good grip.
- G10:
- A high-pressure fiberglass laminate. It is lightweight, durable, and resistant to moisture.
- Carbon Fiber:
- Lightweight, strong, and has a modern, high-tech appearance.
- Stabilized Wood:
- Wood that has been impregnated with resin to improve durability and resistance to moisture.
- Bone and Horn:
- Traditional materials that add a unique and natural aesthetic.
- Titanium:
- Lightweight and corrosion-resistant. Often used for high-end custom knife handles.
Other Components:
- Bolsters:
- Metal components, often placed at the ends of the handle for added strength and aesthetics.
- Pins and Rivets:
- Used to secure the handle scales to the tang and add structural integrity.
- Liners:
- Thin layers of material (often contrasting in color to the handle) used between the scales for visual appeal.
- Sheath Material:
- Leather, Kydex, or other materials can be used for making a sheath to protect and carry the knife.
Custom knife makers often experiment with different combinations of these materials to create unique and functional knives. It’s essential to consider the balance between aesthetics, functionality, and the specific needs of the user when selecting materials for a custom knife.